Why Choose Our Services
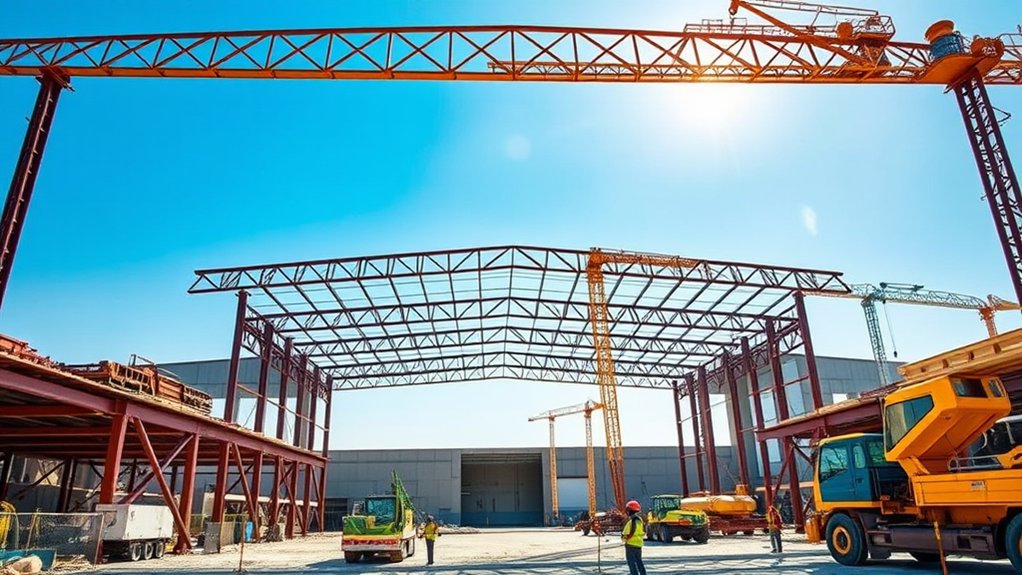
Selecting the right construction partner can greatly impact the success of a warehouse project in Rabigh. A strategic choice can guarantee adherence to timelines, budgets, and quality standards, which are crucial for operational efficiency.
Selecting a partner with a proven track record minimizes risks associated with delays or subpar construction practices. Key considerations include the partner's experience in warehouse construction, familiarity with local regulations, and capacity to manage complex projects.
Effective communication is essential, allowing for adjustments and proactive problem-solving throughout the project lifecycle. Additionally, a reliable partner offers insights into innovative solutions and best practices, empowering clients to make informed decisions.
Ultimately, the right construction partner enhances control over project outcomes, guaranteeing a successful warehouse build tailored to specific needs.
Our Expertise & What We Offer
Leveraging extensive industry experience, the construction team specializes in warehouse projects tailored to the unique demands of Rabigh. Their approach is grounded in meticulous planning and execution, ensuring each project aligns with specific client requirements.
The team offers all-encompassing services, from initial design consultations to final construction oversight, allowing clients to maintain control throughout the process. Emphasizing quality and efficiency, they utilize advanced construction techniques and materials to optimize durability and functionality.
Additionally, the construction team prioritizes adherence to timelines and budgets, ensuring that every project is delivered as promised. With a commitment to excellence, they empower clients with insights and updates, fostering transparency and confidence in every phase of the warehouse construction journey.
Industries We Serve
The construction team's expertise is prominently showcased in the steel industry, particularly in Saudi Arabia. They address the unique needs of clients within this sector by providing tailored solutions that enhance operational efficiency.
With a deep understanding of the requirements specific to steel production, the team designs robust facilities that support heavy machinery and streamline manufacturing processes. These specialized constructions not only comply with industry regulations but also ensure maximum productivity and operational control.
Benefits of Professional Services
While engaging professional services in warehouse construction, companies can greatly enhance project outcomes and operational efficiencies.
These services provide expertise in design, planning, and execution, ensuring that projects are completed on time and within budget. Professionals utilize advanced technologies and methodologies, leading to improved accuracy in construction and reduced risks.
Moreover, their experience allows for effective problem-solving, minimizing potential disruptions during the project. By maintaining strict adherence to regulatory standards, companies can avoid costly delays caused by compliance issues.
Additionally, professional services offer insights into optimizing warehouse layouts for maximum productivity.
Ultimately, leveraging these specialized services not only streamlines the construction process but also positions companies for long-term success in their operational goals.
How Our Process Works
Understanding how the construction process unfolds is essential for companies embarking on a warehouse project with Saudi Steel Work. The process begins with a detailed site assessment, allowing for an evaluation of specific needs and potential challenges.
Next, comprehensive planning is conducted, involving timelines, budget estimates, and resource allocation, ensuring that every aspect is accounted for. Following the planning phase, permits and approvals are secured to comply with local regulations.
Once authorized, construction commences, utilizing a methodical approach to maintain quality and efficiency. Regular progress updates are provided, allowing stakeholders to monitor developments closely.
Finally, upon completion, a thorough inspection guarantees that all specifications have been met, empowering companies to take full control of their new warehouse operations from day one, all facilitated by Saudi Steel Work.
Find the Best Steel Company Near You
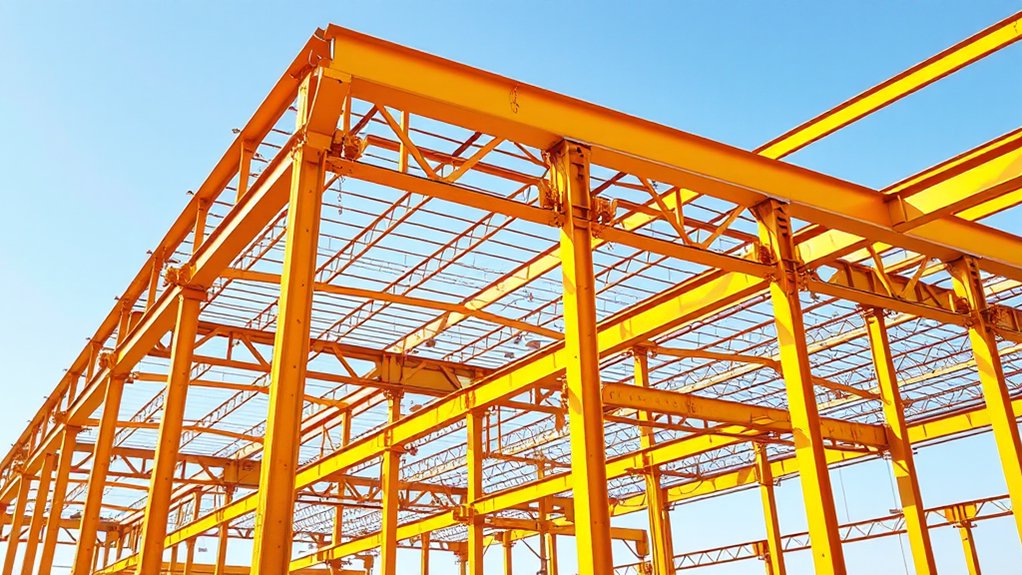
Neighbourhoods We Serve
Name | Zip Code |
---|---|
Riyadh | 11564 |
Jeddah | 21577 |
Dammam | 31461 |
Khobar | 31952 |
Mecca | 21955 |
Medina | 42311 |
Tabuk | 71411 |
Abha | 62521 |
Khamis Mushait | 62413 |
Al Khobar | 31952 |
Choosing the right steel company can greatly impact the success of a warehouse construction project. A strategic approach involves researching local steel suppliers to identify those with a strong reputation for reliability and service. Prospective clients should evaluate each company's portfolio, ensuring past projects align with their specific needs. Engaging directly with representatives can provide insight into their capabilities and responsiveness. Additionally, obtaining multiple quotes allows for an informed comparison of pricing and services. It is essential to assess the company's delivery timelines, as delays can hinder project progress. By prioritizing communication and clarity in expectations, clients can select a steel company that not only meets their requirements but also contributes positively to the overall construction outcome.
Quality & Standards
Ensuring high quality and adherence to industry standards is crucial in warehouse construction, particularly within the steel industry in Saudi Arabia. At Saudi Steel Work, we recognize that these factors directly influence the durability and safety of the structures we build.
The implementation of rigorous quality control measures throughout the construction process is essential. This involves selecting materials that meet specified certifications and employing skilled labor to execute precise construction techniques. Compliance with local building codes and international safety standards further reinforces structural integrity.
Regular inspections and assessments are conducted to identify any deviations from established protocols, ensuring that our projects meet the highest standards.
Additionally, adopting best practices in project management, including detailed planning and risk assessment, helps maintain control over quality outcomes. Ultimately, our commitment to high standards not only enhances operational efficiency but also safeguards investments in warehouse facilities in Rabigh, reinforcing our position as a leader in the steel industry.
Frequently Asked Questions
What Is the Average Timeline for Warehouse Construction Projects?
The average timeline for warehouse construction projects typically spans from six months to two years. Factors influencing this duration include project size, complexity, permitting processes, and local regulations, which can greatly impact overall construction schedules.
How Do Weather Conditions Affect Construction Schedules in Rabigh?
Weather conditions greatly influence construction schedules, often causing delays. Rain, extreme temperatures, and wind can hinder progress, necessitating careful planning and adjustments to timelines to guarantee safety and project efficiency throughout the construction process.
Are There Any Local Regulations Specific to Warehouse Construction?
Local regulations governing construction typically encompass zoning laws, building codes, and environmental standards. These regulations aim to guarantee safety, sustainability, and compliance, thereby empowering stakeholders to navigate the complexities of construction effectively and responsibly.
What Are Common Materials Used in Warehouse Construction?
Common materials utilized in warehouse construction include steel for structural frames, concrete for flooring and walls, and insulation materials for temperature control. These choices reflect durability, efficiency, and adaptability, ensuring ideal functionality for diverse storage needs.
Can I Customize the Design of My Warehouse?
Customization of a warehouse design is indeed possible. Clients can specify layout, materials, and features, ensuring the structure meets their operational needs and preferences, ultimately providing greater control over functionality and aesthetic appeal.